In manufacturing, time truly is money. Every minute your production line is down, your bottom line takes a hit. Yet many facilities don’t fully realize the true cost of downtime—or worse, they wait until something breaks before taking action. At Sonic Tools, we’ve seen how proactive planning and proper tooling can dramatically reduce downtime and keep operations running at peak performance.
What is Downtime in Manufacturing?
Manufacturing Downtime refers to any period when production stops due to equipment failure, maintenance, supply issues, or human error. It can be planned (like scheduled maintenance) or unplanned (like a sudden machine breakdown). It’s the unplanned variety that’s the most costly—and often the most preventable.
The Hidden Costs of Downtime
Many manufacturers look at downtime as simply “lost production,” but its impact goes far beyond that. Here’s what it really costs:
Lost Revenue
When machines stop, so does output. That means orders go unfulfilled, deadlines get pushed, and customer satisfaction suffers. Depending on the size of your operation, even one hour of downtime can result in thousands—or even millions—of dollars in lost revenue.
Labor Inefficiencies
You’re still paying your team even if they can’t work. Idle labor during breakdowns is wasted payroll. Plus, scrambling to fix the problem often leads to overtime costs and low morale.
Emergency Repairs
When equipment breaks unexpectedly, repair costs spike. Rush orders for parts, expedited shipping, and emergency labor all add up—often far exceeding the cost of regular preventative maintenance.
Safety Risks
Unplanned breakdowns can create hazardous situations on the floor. Faulty tools, overloaded systems, or improvised fixes increase the risk of injury—and the cost of liability.
Reputational Damage
Failing to deliver on time or compromising product quality can damage your brand’s reputation. Clients and partners may start looking elsewhere, costing you future business.
Why Planning Ahead Matters
The most effective way to minimize downtime is to plan for it before it happens. Here’s how Sonic Tools helps manufacturers do just that:
Tool and Inventory Control
With our custom foam inlays and durable toolboxes, you always know where your tools are—and what’s missing. That means less time spent searching and more time fixing the problem fast.
Preventative Maintenance Support
Our standardized toolsets help maintenance teams follow consistent routines and catch small issues before they become major problems. When everyone has the right tools and knows exactly where they are, preventative maintenance becomes second nature.
Mobile Access for Fast Repairs
Sonic’s mobile workstations bring the tools to the problem, reducing delays caused by running back and forth to a supply room. That’s critical when every second counts.
Data-Driven Planning
With Sonic’s inventory management systems, you can track tools and forecast needs. This helps you plan maintenance schedules intelligently and replace tools before they fail.
Proactive Maintenance = Uptime and Profit
The most efficient facilities think ahead. They don’t just react to problems — they prevent them. Investing in the right tooling strategy supports your technicians, reduces unplanned stops, and saves real money over time.
With Sonic Tools, you get:
- Faster repair turnaround
- Fewer tool-related delays
- Improved technician productivity
- Safer, more organized work environments
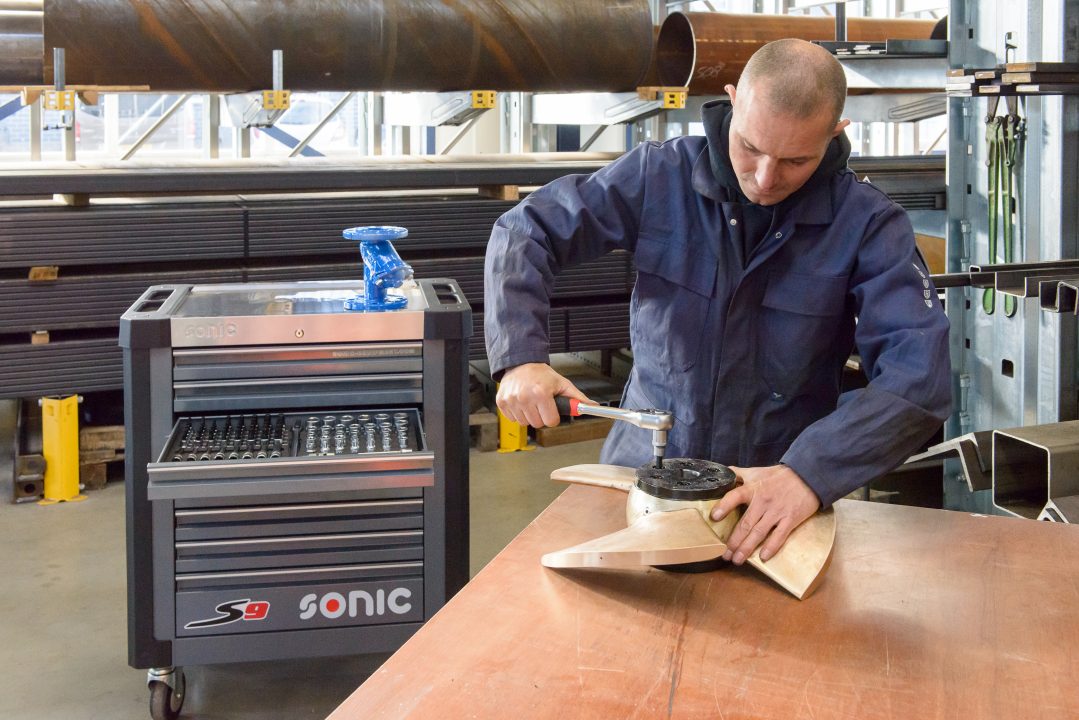
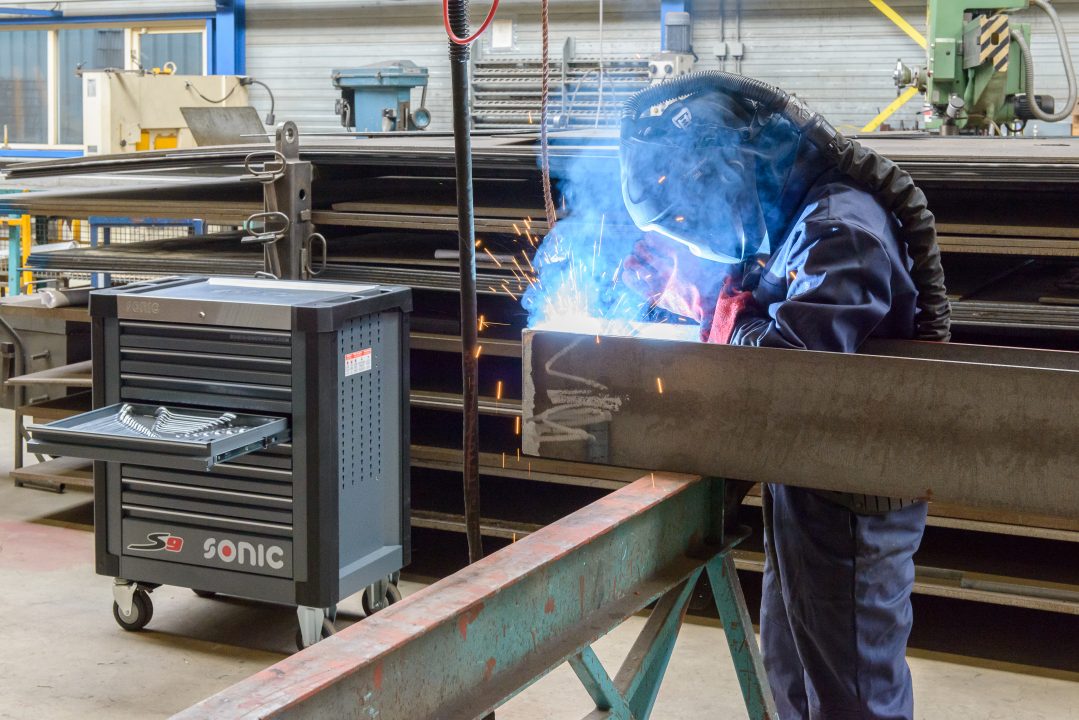
The Bottom Line
Downtime isn’t just a nuisance—it’s a threat to your productivity, profitability, and reputation. The good news? It’s also preventable. By planning ahead, investing in the right tools, and committing to proactive maintenance, you can turn downtime into uptime—and give your team the confidence to operate at full capacity. At Sonic Tools, we’re not just here to equip your toolbox—we’re here to empower your entire operation.
Frequently Asked Questions
Common causes include machine failures, missing tools, human error, and lack of scheduled preventative maintenance.
Through foam inlays, mobile storage, and standardized toolkits that keep maintenance teams efficient and responsive.
Planned downtime is scheduled (e.g., maintenance windows); unplanned downtime occurs unexpectedly and usually costs more.
Yes. Organized, etched tools improve accountability and help prevent accidents from faulty or missing equipment.
Contact our team to assess your tool needs and implement a solution tailored to your workflow and maintenance program.