Sonic Keeps Your Facility Running
In the world of manufacturing, downtime is death. Manufacturers who adopt preventative maintenance strategies, and don’t carry their strategy down to the tooling solution for the facility should not consider themselves immune from a work stoppage.
Sonic tools are designed for one thing. Efficiency. Our tools and toolboxes, when paired with the innovative Sonic Foam System (SFS), are the epitome of 5S manufacturing practices. Companies invest tens of thousands in 5S practices that include efficient tooling as part of their strategy position themselves in much safer waters.
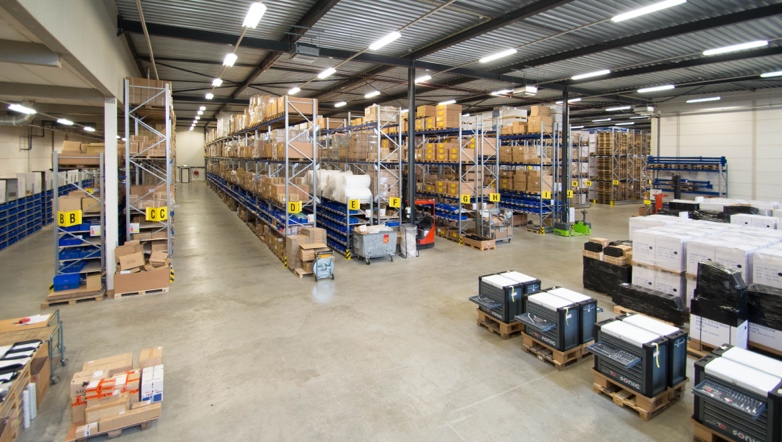
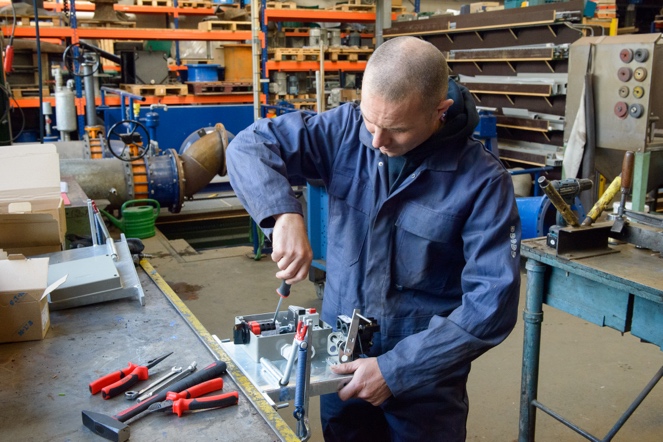
The True Cost of Downtime
- Financial Impact: The potentially massive financial impact of unplanned downtime in manufacturing cannot be understated. Idle machinery means lost production capacity, unmet deadlines, and delayed deliveries.
- Decreased Productivity: Beyond the immediate loss of output, unplanned downtime disrupts workflow and erodes productivity. Production schedules are thrown off, and employees may be left waiting for machines to be operational again.
- Quality Control and Rework: Rushed production to compensate for lost time of unplanned downtime can compromise product quality. When machines unexpectedly stop mid-production, defects and errors increase.
- Maintenance Costs: Reactive maintenance following unplanned downtime often comes with a hefty price tag. Emergency repairs can be more expensive than routine maintenance performed during planned downtime.
- Supply Chain Disruptions: Unplanned downtime doesn’t only affect the manufacturing facility itself, but there is a ripple across the entire supply chain. Production delays can disrupt downstream processes, impacting suppliers, distributors, and ultimately, your customers.
- Loss of Customer Confidence: Maintaining customer confidence is crucial for long-term success for manufacturing businesses. Unplanned downtime can result in missed delivery deadlines, leaving customers dissatisfied and seeking alternative suppliers.