Introduction
In the fast-paced world of manufacturing, efficiency is not just a goal but a necessity for success. Every wasted minute translates to lost productivity and potential revenue. This is where the principles of 5S and lean manufacturing come into play. With Sonic, manufacturers can elevate their processes to new heights. The 5S methodology – Sort, Set in Order, Shine, Standardize, and Sustain – is a cornerstone of lean manufacturing. This systematic approach organizes and standardizes the workplace for enhanced efficiency, safety, and productivity. While the concept is straightforward, effective implementation requires the right tools and commitment.
Best Practices for 5S Success
- Sort: Begin by decluttering and organizing tools and equipment. Identify and remove unnecessary items from the workspace to create a clean and efficient environment. This step helps in minimizing clutter and optimizing space usage.
- Set in Order: Arrange the remaining items logically and efficiently. Utilize Sonic’s lean tool storage solutions to ensure each tool has a designated place, promoting easy access and rapid retrieval. Labeling and visual cues are crucial in this step.
- Shine: Maintain cleanliness and orderliness in the workspace to uphold safety standards and boost morale. Sonic’s high-quality materials and durable construction ensure that tools remain pristine with minimal maintenance. Regular cleaning schedules are essential to sustain this practice.
- Standardize: Establish standardized procedures and protocols for organizing and maintaining the workspace. Sonic uses innovative solutions such as standard serialization and laser etching on hand tools within our toolsets. We use high-powered fiber-optic lasers to etch the metal, creating a permanent marking on each tool, ensuring no cross-contamination and consistent quality.
- Sustain: Continuously monitor and improve 5S practices to ensure long-term success. Sonic’s nationwide support and global network provide manufacturers with the assistance they need to sustain efficiency gains and overcome challenges as they arise.
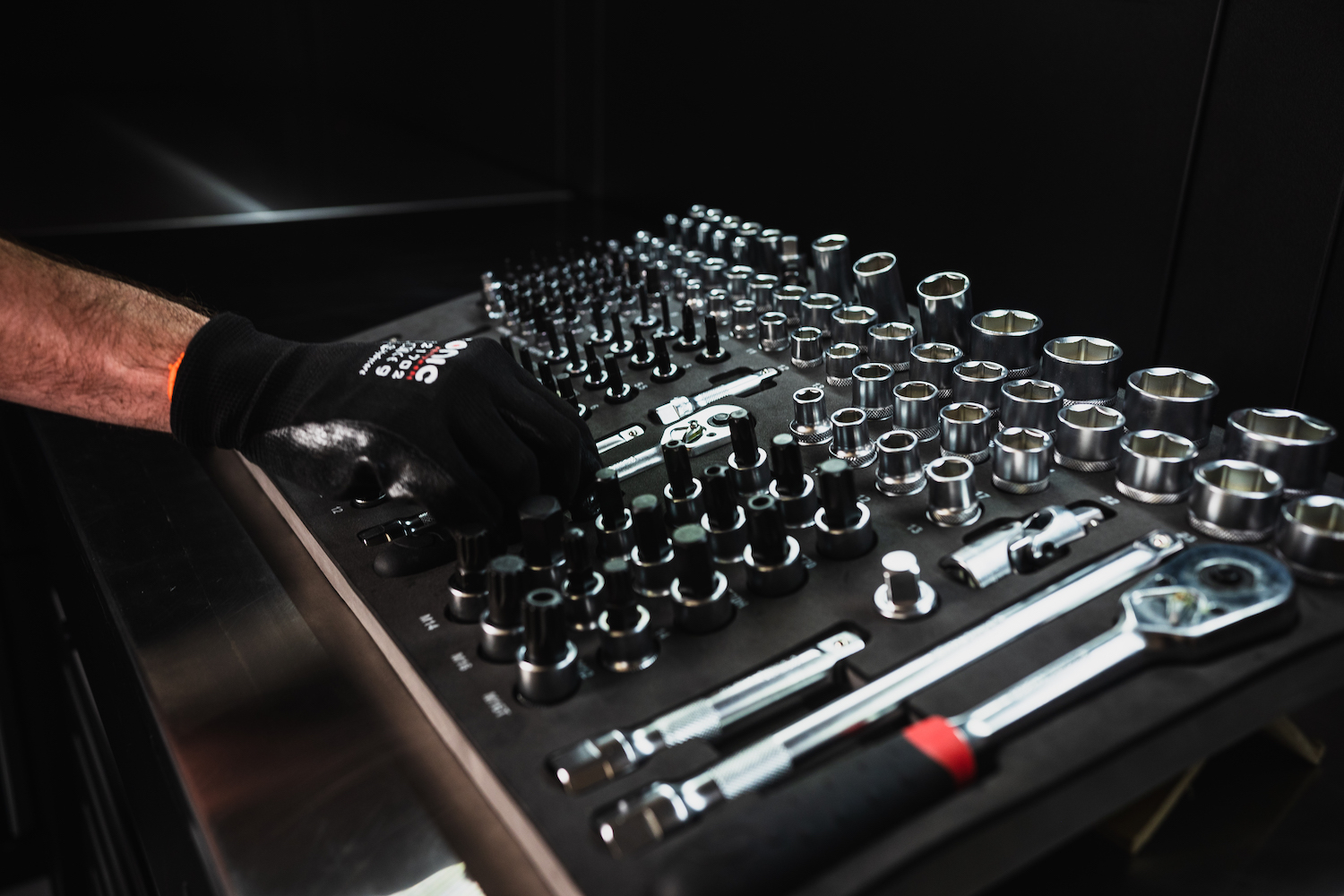
Tools for 5S Excellence
- Sonic Foam System (SFS): The Sonic Foam System is identified clearly with a two-tone system for easy reference of any missing tools and is chemical resistant. These inserts enable precise organization of tools, ensuring each item has a designated place within the workspace. This minimizes time wasted searching for tools and enhances visual management, promoting adherence to 5S principles.
- Lean Tool Storage Solutions: Our toolboxes, cabinets, and workstations are designed to optimize space and promote efficient tool storage. With ergonomic designs and customizable configurations, these solutions support the “Set in Order” pillar of 5S, facilitating easy access and retrieval of tools.
- Comprehensive Toolsets: Sonic’s Pathway Program offers comprehensive toolsets tailored to specific industries and applications. With our Sonic Pathway Program’s Basic, Intermediate, and Advanced levels, technicians can get the necessary tools without having too many or too few. This ensures they have precisely the tools they need when they need them, supporting the “Sort” and “Standardize” pillars of 5S.
- Streamlined Support: Sonic’s commitment to customer satisfaction extends beyond product offerings. We provide a lifetime, hassle-free warranty, ensuring your new replacement tool is dispatched within 24 hours. With dedicated support teams and a single point of contact, facilities & technicians can rely on Sonic for guidance, assistance, and expertise throughout their 5S journey.
Conclusion
Incorporating 5S practices into your manufacturing processes is essential for driving efficiency and achieving operational excellence. Sonic provides the best practices and tools to optimize your facility’s 5S processes and empower technicians to succeed in today’s competitive landscape. Explore the transformative impact of the Sonic Foam System and increase your operational efficiency.